In construction, success hinges on preparation. One of the most impactful prep steps a construction project manager can take is prequalifying subcontractors. This process isn’t just a box to check before breaking ground: it’s a vital risk management tool that can make or break a project.
Whether you’re overseeing a residential development, a commercial build, or a large-scale infrastructure project, the subcontractors you bring on board set the tone for safety, quality, and efficiency.
The Strategic Value of Subcontractor Prequalification
Subcontractor prequalification is the process of thoroughly vetting potential partners before awarding them a contract. This assessment spans financial health, safety records, regulatory compliance, project experience, and more. In essence, it’s a proactive approach to ensuring that every party on a job site is up to the task and equipped to meet the project’s standards from day one.
Rather than reacting to problems as they arise, prequalification allows construction firms to avoid issues altogether by selecting the most competent, qualified, and dependable subcontractors from the start.
1. Minimizing Project Risks
Construction projects are inherently complex and unpredictable. From supply chain disruptions to labor shortages, risk is everywhere. However, hiring unqualified or unverified subcontractors introduces preventable risks that can have cascading consequences:
- Delays: Subcontractors without proper staffing, experience, or financial backing may fall behind schedule, delaying project milestones.
- Quality Issues: Inexperienced subcontractors may deliver substandard work, resulting in costly rework or structural concerns.
- Safety Hazards: Poor safety practices can lead to accidents, regulatory fines, or even job site shutdowns.
Through prequalification, you can assess a subcontractor’s ability to adhere to timelines, meet quality benchmarks, and maintain safety protocols, all before a contract is signed.
2. Ensuring Regulatory and Industry Compliance
Construction is one of the most heavily regulated industries in the world. Federal, state, and local codes must be followed, as well as OSHA standards, environmental regulations, and union agreements in many cases.
Prequalifying subcontractors ensures that:
- They possess up-to-date licenses and permits.
- Their certifications are current and relevant to the job at hand.
- They understand and are committed to following all applicable regulations.
By verifying compliance early, you reduce the risk of fines, litigation, and project halts down the line.
3. Improving Overall Project Outcomes
A subcontractor with the right expertise, resources, and approach can elevate an entire project.
Prequalified subcontractors are more likely to:
- Work collaboratively with other subcontractors.
- Communicate effectively and proactively.
- Anticipate potential challenges and solve problems quickly.
- Deliver work that meets or exceeds expectations.
Ultimately, when your team is built with capable, vetted professionals, you’re setting your project up for success.
Key Criteria for Subcontractor Prequalification
A comprehensive prequalification process should include multiple evaluation points to ensure a subcontractor is truly ready to perform. Consider the following areas:
Experience and Project History
Has the subcontractor successfully worked on similar projects? Reviewing case studies, portfolios, and past client testimonials provides insight into whether the subcontractor has the right kind of experience.
Financial Stability
Financial strength is non-negotiable. A subcontractor must have the resources to manage cash flow, cover payroll, and purchase materials.
Evaluate their:
- Financial statements
- Bonding capacity
- Credit ratings
These metrics signal whether a subcontractor can sustain operations throughout the project’s duration.
Safety Records and EMR (Experience Modification Rate)
A strong safety record is both a legal and moral imperative.
Prequalify subcontractors based on:
- OSHA recordables
- EMR ratings
- Safety program documentation
- Training certifications
An unsafe subcontractor can put lives at risk and lead to insurance claims or legal repercussions.
Certifications and Licenses
Ensure that subcontractors hold all the required certifications for the type of work you need done.
Examples include:
- General subcontractor licenses
- Trade-specific certifications (e.g., electrical, HVAC, plumbing)
- Minority-owned business certifications (if required for public projects)
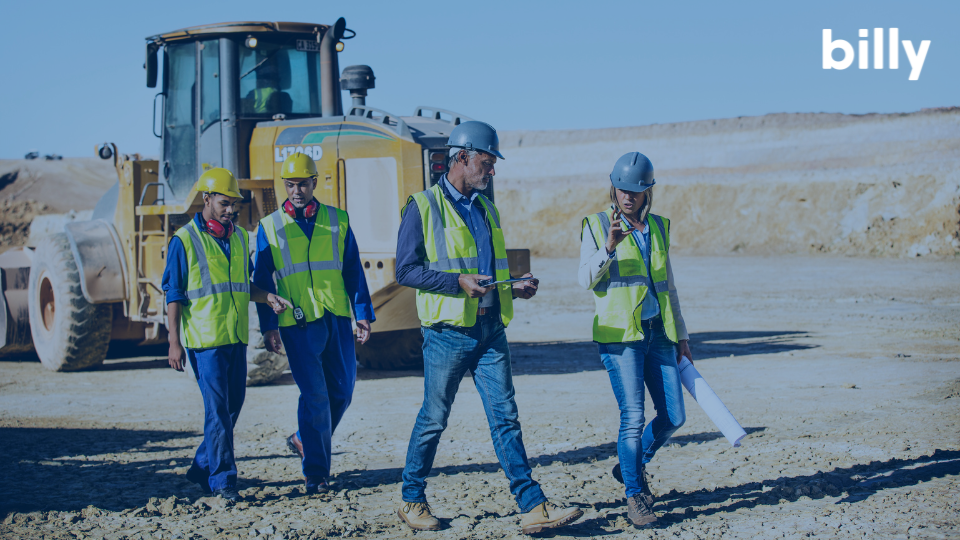
References and Reputation
Reach out to former clients, architects, engineers, or even other subcontractors. What was their experience? Would they work with this subcontractor again?
The Role of Technology in Streamlining Prequalification
Manual prequalification processes can be time-consuming, error-prone, and difficult to scale. That’s where digital tools come in.
Faster Data Collection and Review
Digital platforms allow for centralized data submission, with subcontractors uploading all necessary documentation directly. This eliminates back-and-forth emails and misplaced paperwork.
Automated Compliance Checks
Billy developed a subcontractor prequalification tool that automatically flags missing documents, expired licenses, or low safety scores. This gives compliance teams the confidence that no detail is overlooked.
Easier Collaboration
With cloud-based systems, multiple team members can review subcontractor qualifications in real-time, provide feedback, and track approvals, all from one platform.
Better Record Keeping
Digital storage ensures that documentation is organized, searchable, and readily available during audits or future project planning.
Best Practices for Implementing Subcontractor Prequalification
1. Establish Clear Criteria and Standardization
Develop a standardized checklist or scoring rubric for subcontractor evaluation. This promotes fairness, transparency, and consistency.
2. Use a Centralized Prequalification Platform
Software like Billy makes it easy to collect, verify, and assess subcontractor data in one place. It reduces the administrative burden on your team and increases confidence in your hiring decisions.
3. Review and Refresh Regularly
Prequalification isn’t a one-and-done process. Subcontractors’ financial situations, staff, and compliance statuses change. Requalify long-term partners annually or before each new project.
4. Train Your Team
Ensure your compliance and project management teams are trained on both your internal process and the prequalification software. This ensures consistency and efficient decision-making.
Final Thoughts: Build Better Projects by Starting with Better Partners
Prequalifying subcontractors isn’t just a safety net—it’s a strategic advantage. It ensures that every professional on your site is vetted, capable, and ready to contribute to your project’s success. By investing time upfront to assess subcontractor credentials, you’re protecting your budget, your timeline, and your team.
Today’s construction leaders are embracing digital tools to make this process faster and smarter. If you’re ready to modernize your contractor vetting process, Billy offers an intuitive prequalification tool that simplifies compliance, automates documentation reviews, and ensures you’re always working with the right partners.
Ready to reduce risk and streamline your subcontractor onboarding?
Start using Billy’s prequalification tool today to evaluate, verify, and manage contractor compliance—all in one easy-to-use platform. Schedule a free demo today to learn more!
Frequently Asked Questions
Prequalifying a subcontractor involves evaluating their experience, safety history, financial stability, licenses, and references. Many companies use digital tools (like Billy) to streamline this vetting process and ensure compliance before work begins.
Key information includes proof of licensing and insurance, financial records, safety statistics (like EMR and OSHA logs), project history, and client references. This data helps assess a subcontractor’s ability to perform safely and reliably.
Subcontractors often use construction management platforms for scheduling, documentation, and compliance tracking. Tools like Billy simplify prequalification by helping contractors securely submit credentials and track COIs in one place.